API 5L X70 Line Pipe Introduction
API 5L X70 line pipe is a high-strength, high-toughness steel pipe widely used in the transmission of oil, gas, and water over long distances. The “X70” designates a minimum yield strength of 70,000 psi (485 MPa).
Dimension Range of API 5L X70 Pipes (Seamless and Welded)
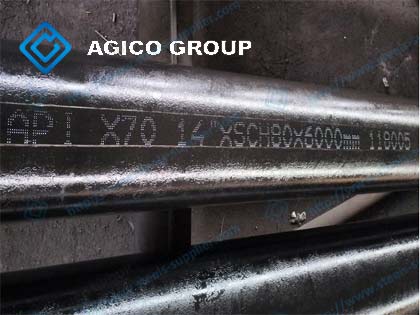
Pipe Type | Outer Diameter (OD) | Wall Thickness (Schedule) |
---|---|---|
Seamless | ½″ – 24″ (12.7 mm – 610 mm) | Sch 10 – Sch 160, STD, XS, XXS |
Welded (ERW/LSAW/DSAW/SSAW/HSAW) | ½″ – 48″ (12.7 mm – 1219 mm) | Sch 10 – Sch 160, STD, XS, XXS |
API 5L X70 Specification Introduction
API 5L X70 is a steel grade of carbon steel pipe standard widely used in oil and gas pipeline systems. As part of the API 5L specification developed by the American Petroleum Institute (API), Grade B pipe is suitable for transporting natural gas, petroleum products and water, and has 2 specification levels: PSL1 and PSL2. PSL2 has more stringent requirements in chemical composition control, mechanical property testing, non-destructive testing and quality traceability.
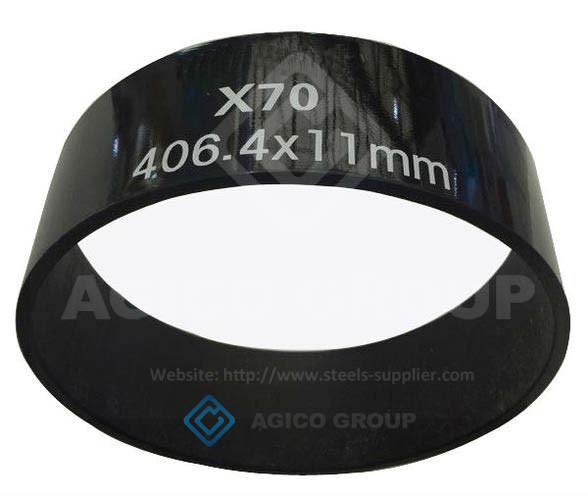
- Standard: API 5L (version number must be specified, such as 46th edition or latest edition)
- Grade: X70
- Product Specification Level: PSL1 (basic requirements) / PSL2 (additional more stringent requirements)
- Manufacturing process: seamless (SMLS), electric resistance welding (ERW), straight seam submerged arc welding (LSAW), spiral submerged arc welding (SSAW)
- Main applications:API 5L Grade X70 PSL1 Pipe Suitable for Conveying gas, water, oil, and other liquefied media in Oil Refineries, Petrochemicals, Steel, Sugar, Boiler Equipments, Pressure Vessels, Power Generation (Nuclear/Thermal) and General Engineering Purposes
Common Types of API 5L X70 Line Pipe:
API 5L X70 line pipes are available in both seamless and welded formats, covering a wide range of diameters and wall thicknesses. Multiple PSL levels including sour-service grades ensure adaptability to harsh environments. Welding methods cater to a wide range of project requirements, while PSL2 provides enhanced quality control for critical applications.
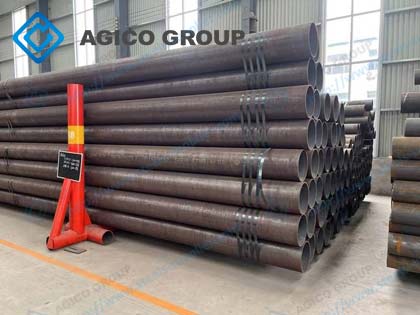
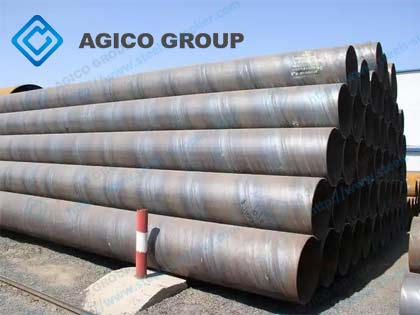
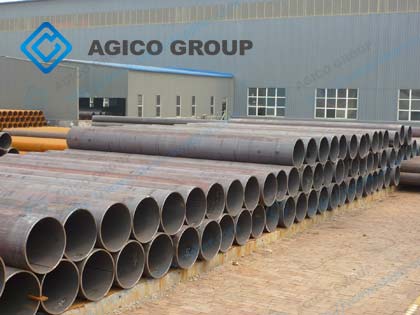
- Seamless pipes are often the first choice for high-pressure, critical operations and smaller diameters due to their integrity.
- Welded pipes (ERW, LSAW, SSAW) are widely used for larger diameter pipelines and have cost-effective advantages.
API 5L X70 Specification:
API 5L X70 PSL1 and PSL2 Chemical Composition:
The chemical composition of API 5L X70 slightly between PSL1 and PSL2. PSL2 varies stricter controls to improve toughness and weldability.
API 5L X70 PSL 1 | ||||||||
---|---|---|---|---|---|---|---|---|
Grade | Composition, % | |||||||
C max | Mn max | P | S max | V max | Nb max | Ti max | ||
min | max | |||||||
B | 0.28 | 1.2 | – | 0.03 | 0.03 | c.d | c,d | d |
X70 | 0.28 | 1.4 | – | 0.03 | 0.03 | f | f | f |
API 5L X70Q PSL 2 | |||||||||
---|---|---|---|---|---|---|---|---|---|
Grade | Composition, % | ||||||||
C | Si | Mn | P | S | V | Nb | Ti | Other | |
X70Q | 0.18 | 0.45 | 1.8 | 0.025 | 0.015 | g | g | g | h,l |
Note: PSL2 restricts harmful elements and controls CEq to improve weldability and fracture toughness.
Seamless and Welded X70 Line Pipe Mechanical Property
Pipe Grade | Tensile Properties -PSL1 X70 Pipe Body of SMLS and Welded Pipes | Seam of X70 Welded Pipe | ||
---|---|---|---|---|
Yield Strength a | Tensile Strength a | Elongation | Tensile Strength b | |
Rt0,5 PSI Min | Rm PSI Min | (in 2in Af % min) | Rm PSI Min | |
X70 | 70,300 | 82,700 | c | 82,700 |
Pipe Grade | Tensile Properties -PSL2 X70 Pipe Body of SMLS and Welded Pipes | Seam of X70 Welded Pipe | |||||
---|---|---|---|---|---|---|---|
Yield Strength a | Tensile Strength a | Ratio a,c | Elongation | Tensile Strength d | |||
Rt0,5 PSI Min | Rm PSI Min | R10,5IRm | (in 2in)Af % | Rm (psi) | |||
Minimum | Maximum | Minimum | Maximum | Maximum | Minimum | Minimum | |
X70Q | 70,300 | 92,100 | 82,700 | 110,200 | 0.93 | f | 82,700 |
Manufacturing of API 5L X70 PSL2 Line Pipe
There are TMCP and Q&T technologies suitable for manufacturing of API 5L X70 line pipes, for psl1 and psl2 welded pipes, pipt types are produced in different welding methods and supplied to customers.- Controlled rolling, thermomechanical controlled process (TMCP), or quenching and tempering (Q&T).
- Heat treatment must be recorded and traceable.
Technology | Applicable scenarios | Performance Advantages |
---|---|---|
TMCP | Wall thickness ≤40 mm | High toughness + good weldability |
Q&T | Wall thickness > 40 mm/high pressure | Uniform structure + low residual stress |
Type of Pipe | PSL 1 | PSL 2 |
---|---|---|
X70 | X70Q | |
SMLS | ✔ | ✔ |
LFW | ✔ | |
HFW | ✔ | ✔ |
LW | ✔ | |
SAWL | ✔ | ✔ |
SAWH | ✔ | ✔ |
SMLS – Seamless, without weld LFW – Low frequency welded pipe, <70 kHz HFW – High frequency welded pipe, >70 kHz SAWL – Submerge-arc welding longitudinal welded SAWH - Submerge-arc welding helical welded |
Delivery Condition
API 5L X70 Line Pipes are available in 2 classes: psl1 and psl2, AGICO supplies full size range of API 5L pipes in following delivery conditions.
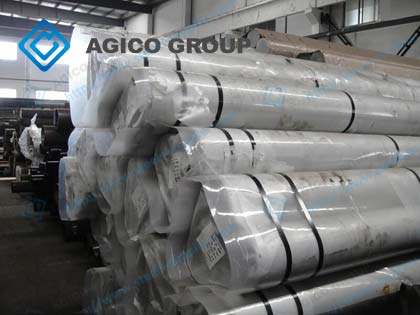
API 5L X70 Line Pipe Package
PSL | Delivery Condition | Pipe grade |
---|---|---|
PSL 1 | As-rolled, normalizing rolled, thermomechanical rolled, thermo-mechanical formed, normalizing formed, normalized, normalized and tempered | X70 |
PSL 2 | Quenched and tempered | X70Q |
Thermomechanical rolled or thermomechanical formed | X70M |
Welding Process Limitations
API 5L X70 can be produced by different manufacturing methods depending on the application and requirement:
- ERW : Only for DN≤600 mm, pressure≤15 MPa
- SAW (LSAW/DSAW) : Post-weld heat treatment (PWHT) is required + weld toughness matches the parent material
Testing and Requirements for PSL2 X70 Pipe
PSL 2 X70 pipes has better sour environment performance than X70 PSL 1 pipes, they must be tested in the following methods:
Test Type | PSL2 Requirements | Standard basis |
---|---|---|
Water pressure test | Ptest=1.25×SMYS×tD P test = 1.25× DSMYS × t | API 5L §9.4.3 |
AUT Testing | Defect size: Depth > 5% of wall thickness or length > 50 mm will be rejected | API 5L App.U U4 |
DWTT | -15°C Shear area ≥85% (mandatory for thick wall tubes) | API 5L App.I |
HIC Test | CLR≤15%, CTR≤5%, CSR≤2% (NACE TM0284 A solution) | NACE TM0284-2016 |
Typical Application of API 5L X70 Line Pipe
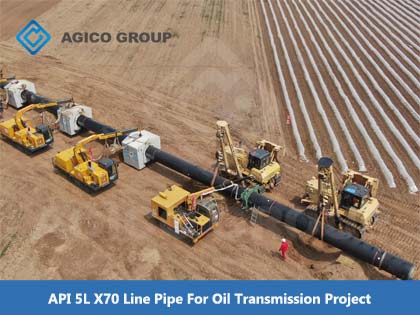
API 5L X70 Line Pipe Project
API 5L X70 is commonly used in oil & gas transmission pipelines, natural gas distribution systems, offshore pipeline construction, hydraulic and water transport systems, high-pressure environments, arctic/subsea installations (with CVN-tested PSL2), basically it is applied to severe working conditions according to PSL level differentiation (PSL2 is a mandatory selection scenario):
Application Areas | Technical basis | PSL Level Requirements |
---|---|---|
Onshore high pressure main pipeline network | Design pressure ≥12 MPa | PSL1/PSL2 |
Submarine pipeline (water depth > 500m) | DNVGL-ST-F101 Strain Design | PSL2 + CTOD ≥ 0.15 mm |
Acidic environment (containing H₂S ) | NACE MR0175 Compliance + HIC Testing | PSL2 |
Arctic low temperature transportation (-60℃) | Base material CVN@-60℃ ≥60J | PSL2 + TMCP process |
Hydraulic systems (high shock loads) | Transient pressure fluctuation ≤1.5 times the design pressure | PSL1 |
Note: PSL2 applicable scenarios require additional DWTT test (-15 ℃ SA ≥ 85%) and full-scale gas burst test (ISO 3183).
How to Choose APT 5L X70 Pipe for Various Applications
Project Type | Recommended Pipe Type | Typical Size |
---|---|---|
Onshore Transmission | LSAW PSL2 | 20"-48" (WT: 9-20mm) |
Offshore Risers | Seamless PSL2 | 6"-12" (WT: 12-25mm) |
Sour Service | SAWH PSL2 + Q&T | 12"-36" (WT: 15-30mm) |
Water Injection | ERW PSL1 |
2"-8" (WT: 3-8mm) |
Welding and Processing performance of X70 Pipe
1. Weldability
The main welding standards includes girth Weld Procedure Qualification: API 1104 and automatic welding equipment: AWS D10.8
Weldability | Parameter range | Engineering significance |
---|---|---|
Carbon equivalent (CEⅡW) | ≤0.43% (PSL2) | Preheat-free welding is allowed (wall thickness ≤ 25mm) |
Heat input control | 15-35 kJ/cm (SAW) | Preventing HAZ embrittlement |
Crack sensitivity | PCM≤0.23% (anti-cold cracking) | Suitable for field manual welding |
2. Molding
Technology | Key Controls | Performance Guarantee |
---|---|---|
Cold bending | Bending radius ≥18×OD | The tube has no wrinkles and the ovality is ≤1.5% OD |
Thermoforming | Temperature 900-950℃ + water quenching | Strength loss ≤5% |
Diameter expansion | Diameter expansion rate ≤1.2% | Maintaining TMCP tissue stability |
3. Coating and end treatment
Type | Applicable standards | Application Scenario |
---|---|---|
3LPE/3LPP | ISO 21809-1/2 | Submarine pipeline (lifespan ≥ 30 years) |
FBE | CSA Z245.20 | Acidic soil environment |
Bevel processing | ASME B16.25 (30°±2° slope angle) | High pressure pipeline automatic welding |
Thread sealing | API 5B (LTC type) | Low pressure water injection pipeline |
API 5L X70 Pipe Dimensions (Seamless & Welded)
Units: OD (mm) | WT (mm) | Mass (kg/m) | Schedule | Manufacturing Methods
Nominal Pipe Size (NPS) | Outside Diameter (OD) | Common Wall Thickness (WT) | Schedule | Mass (kg/m) | Available Types | Notes |
---|---|---|---|---|---|---|
1/2" | 21.3 | 2.11, 2.77, 3.73 | SCH 40, 80 | 1.08–1.82 | SMLS, ERW | Max PSL2 ERW: DN≤600mm |
3/4" | 26.7 | 2.11, 2.87, 3.91 | SCH 40, 80 | 1.41–2.35 | SMLS, ERW | |
1" | 33.4 | 2.77, 3.38, 4.55 | SCH 40, 80 | 2.17–3.50 | SMLS, ERW | |
2" | 60.3 | 2.77, 3.91, 5.54 | SCH 40, 80 | 4.00–7.77 | SMLS, ERW | |
4" | 114.3 | 3.05, 6.02, 8.56 | SCH 40, 80 | 8.63–24.5 | SMLS, ERW, LSAW | |
6" | 168.3 | 3.40, 7.11, 10.97 | SCH 40, 80 | 14.0–44.5 | SMLS, ERW, LSAW | |
8" | 219.1 | 3.76, 8.18, 12.70 | SCH 40, 80 | 20.0–67.8 | SMLS, LSAW, SAWH | ERW max: NPS 24 |
12" | 323.9 | 4.19, 9.53, 12.70 | SCH 40, 80 | 33.7–102 | LSAW, SAWH | Seamless rare ≥12" |
16" | 406.4 | 4.78, 9.53, 12.70 | SCH 40, 60 | 48.2–128 | LSAW, SAWH | |
20" | 508.0 | 5.54, 9.53, 12.70 | SCH 40, 60 | 69.3–160 | LSAW, SAWH | PSL2 common |
24" | 610.0 | 6.35, 9.53, 14.27 | SCH 40, 60 | 95.8–217 | LSAW, SAWH | |
30" | 762.0 | 6.35, 12.70, 19.05 | – | 121–365 | LSAW, SAWH | Max OD for LSAW: 1420mm |
36" | 914.4 | 7.92, 15.09, 20.62 | – | 178–484 | LSAW, SAWH | Offshore/Arctic projects |
42" | 1066.8 | 9.53, 17.48, 23.83 | – | 252–624 | SAWH (Spiral Welded) | High-pressure transmission |
48" | 1219.2 | 11.91, 19.05, 25.40 | – | 362–760 | SAWH | Max standard OD: 1420mm |
Key Technical Notes:
-
Mass Formula:
Mass (kg/m)=(OD−WT)×WT×0.0246615
*Example: 24" OD 610mm × WT 14.27mm → (610-14.27)×14.27×0.0246615 ≈ 217 kg/m* -
Manufacturing Limits:
-
Seamless (SMLS): Max OD ≈ 24" (610mm), thicker walls (SCH 160/XXS)
-
ERW Welded: Max OD = 24" (610mm), limited to PSL1/low-pressure
-
LSAW/SAWH: OD 18"-1420mm, standard for PSL2 X70 pipelines
-
-
Wall Thickness Ranges:
-
Standard: SCH 40/80 (PSL1)
-
High-Pressure: WT up to 40mm (LSAW for subsea pipelines)
-
Custom WT: Up to 100mm (Q&T process for PSL2)
-
-
Tolerances (API 5L Table 14):
Parameter Seamless Welded OD ±0.75% ±0.50% WT +15%/-10% +15%/-10%
